Kunnen hyperlokale aluminiumwaardeketens worden opgeschaald voor massaproductie?
Een lokaal geproduceerd product kopen, gemaakt van aluminium dat afkomstig is van je vriendelijke lokale ‘boer’—het is een intrigerende gedachte. Maar is het in de praktijk schaalbaar voor massaproductie?
Lokaal voedsel is een concept met een lange traditie. Voedsel dat dicht bij de plek waar het geproduceerd is wordt geconsumeerd, heeft een lagere ecologische voetafdruk en vormt een alternatief voor wereldwijd voedsel, waarbij producten grote afstanden afleggen voordat ze de consument bereiken. Zou dit concept ook toepasbaar zijn op de aluminiumindustrie?
Met het R100-project laat Hydro, het bedrijf waar ik voor werk, zien dat het inderdaad mogelijk is om CO2-arme, gerecyclede aluminiumproducten te maken, waarbij de volledige waardeketen, van stedelijke mijnbouw tot eindproduct, binnen een straal van 100 km plaatsvindt. De transportvoetafdruk van het eindproduct werd met ongeveer 90 procent verminderd. Maar het was ontzettend moeilijk om dit te realiseren. De waarheid is dat er vandaag de dag veel schakels zijn die op elkaar afgestemd moeten worden om dit concept op te schalen. Maar in de toekomst? Dan zou het zeker kunnen werken, met enkele kanttekeningen. Laat me het uitleggen.
De lange reis van schroot
Voor wie niet bekend is met de industrie klinkt het misschien als een alledaagse uitdaging om een eindproduct te maken met zo’n hyperlokale waardeketen. Maar voor iemand die de sector kent, is het een gewaagd idee om een bedrijf te baseren op een aluminiumproduct waarvan alles binnen een straal van 100 km wordt verkregen. Want post-consumer schroot, aluminium dat al een volledig leven heeft gehad als ander product, legt gemiddeld een vrij lange reis af voordat het een aluminiumfabriek bereikt.
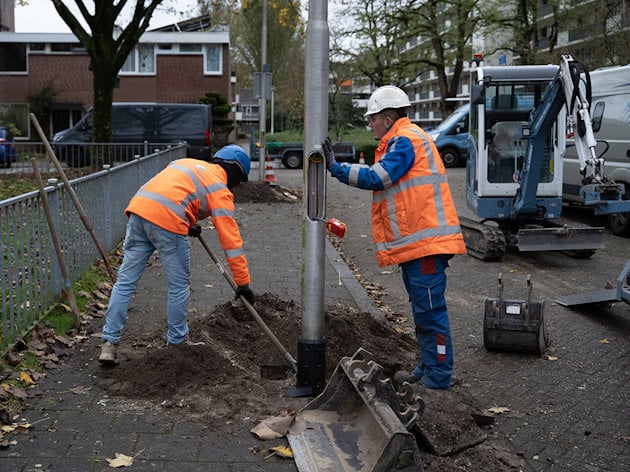
Bij stedelijke mijnbouw wordt aluminium schroot verzameld uit allerlei bronnen waar een aluminiumproduct zijn levenscyclus heeft voltooid. Denk aan een oude kas die wordt afgebroken, lichtmasten die worden verwijderd, of aluminium gevels van een oud hoogbouwpand. Van daaruit gaat het schroot naar een schrootleverancier, die het vervolgens verkoopt aan een gieterij, waar het wordt gesorteerd en opnieuw gesmolten.
We hebben een snelle berekening gemaakt van de gemiddelde gewogen reisafstand van post-consumer schroot naar de gieterijen van Hydro in Europa. In Italië legde het schroot gemiddeld 275 km af over de weg. In België was dat 312 km. In Zweden zelfs 524 km.
Maar in Duitsland was het slechts 100 km. In het Verenigd Koninkrijk 80 km. En in alle landen waren er individuele leveranciers die voldeden aan de maximale afstand van 100 km.
Zoals je ziet, maakt alleen al de afstand tussen schrootleveranciers en gieterijen het concept op dit moment lastig schaalbaar. Maar niet onmogelijk. Er spelen namelijk nog veel meer factoren mee.
Het belang van relaties in de waardeketen
De schrootmarkt is diep geworteld in langdurige persoonlijke relaties tussen schrootleveranciers en hun afnemers, zoals mijn bedrijf. Deze relaties vergen veel tijd en inspanning om op te bouwen en te onderhouden, en zijn essentieel voor een consistente aanvoer en kwaliteitsniveau van post-consumer schroot. Zulke relaties zouden een cruciale rol spelen bij het opschalen van hyperlokale waardeketens.
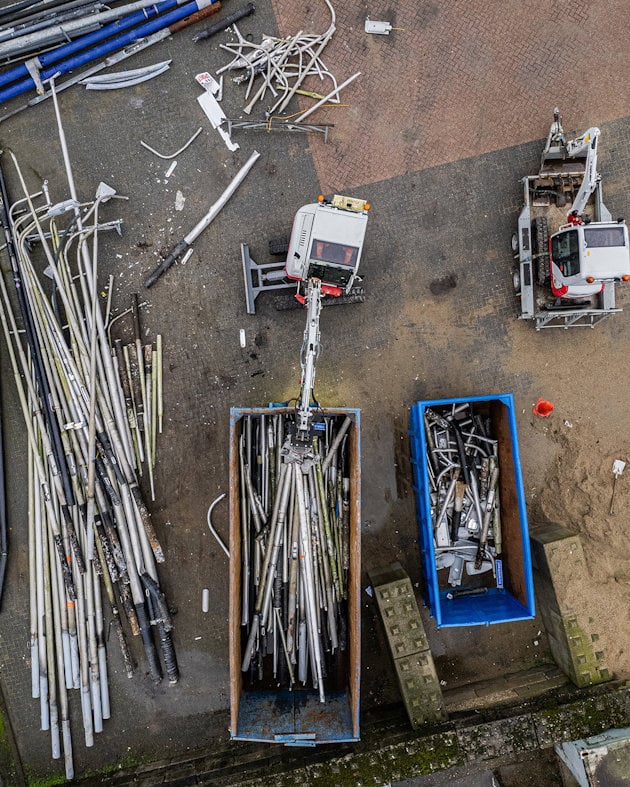
Het serviceniveau van schrootleveranciers, met name wat betreft voorafgaande sortering, heeft een grote invloed op de efficiëntie. Leveranciers die hun schroot grondig voorsorteren, verkorten de verwerkingstijd en verbeteren de materiaalkwaliteit in de gieterij.
Het vermogen om snel beslissingen te nemen wanneer post-consumer schroot (PCS) beschikbaar komt uit sloopprojecten is essentieel. Wendbaarheid en snelle reactie bij het benutten van deze kansen kunnen de continuïteit van de aanvoer aanzienlijk verbeteren. De mogelijkheid om PCS-volumes direct op slooplocaties te reserveren is cruciaal voor het behouden van voorspelbare aanvoerhoeveelheden. Het opzetten van dergelijke reserveringen vereist geavanceerde coördinatie en vertrouwen tussen sloopaannemers en leveranciers.
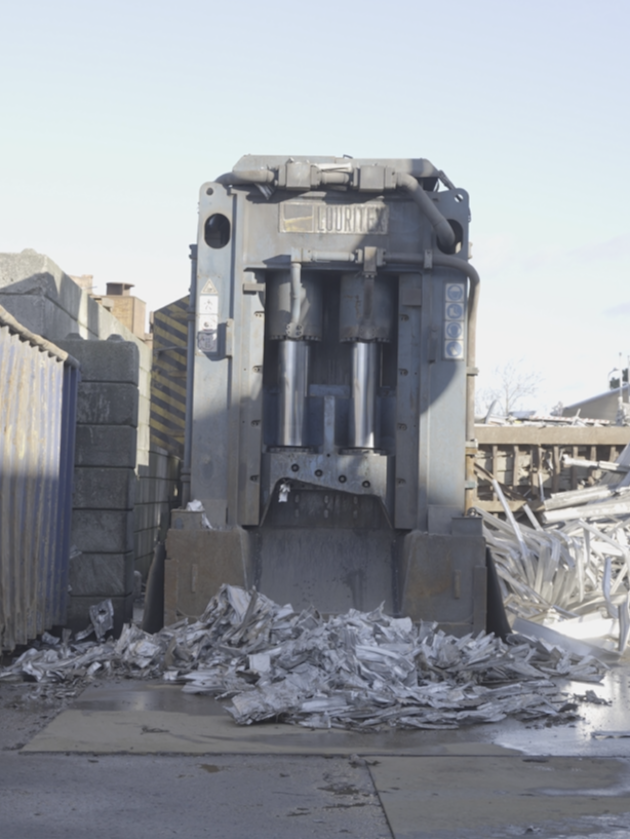
Een ander cruciaal element is het hebben van goed gedefinieerde, schriftelijke werkprocedures en grondige training van medewerkers om inspecties van schrootleveringen uit te voeren en kwaliteitsborging te garanderen. Correcte inspectieprocedures zorgen voor consistente materiaalkwaliteit en verkleinen het risico op vervuiling of verkeerde classificatie.
Deze elementen, die verband houden met de relatie tussen schrootleverancier en klant, zijn een vereiste voor een optimale stroom van lokaal post-consumer schroot. Maar ook aan de kant van de gieterij moeten bepaalde voorwaarden aanwezig zijn.
Operationele uitdagingen bij gieterijen
Aluminium schroot is niet zomaar aluminium schroot. Elk aluminiumproduct heeft een andere legering, waardoor je bijvoorbeeld schroot van lichtmasten niet zomaar kunt mengen met schroot van gevels. Bovendien zitten er aan het meeste schroot nog allerlei onderdelen vast — zoals schroeven, andere metalen, lijmresten enzovoort — die het metaal vervuilen.
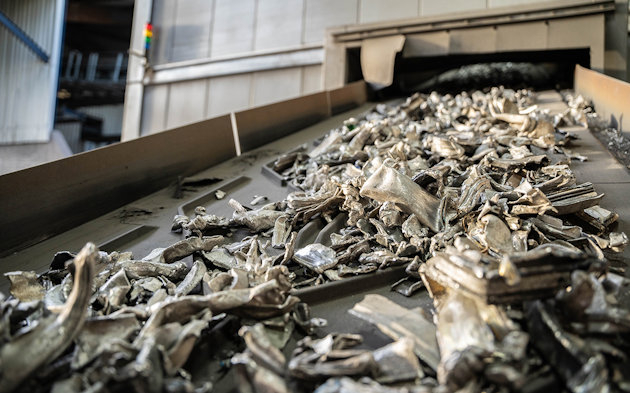
Om dit op te lossen, moeten er geavanceerde fysieke sorteersystemen voor schroot worden geïmplementeerd in de gieterij. Met geavanceerde sorteermogelijkheden kunnen gieterijen gemengd schroot efficiënt verwerken, het hergebruik maximaliseren en verliezen tijdens de verwerking minimaliseren. Daarnaast zijn er voorbehandelingssystemen nodig voor post-consumer schroot vóór het smelten en gieten. Technische installaties moeten aanwezig zijn om het schroot te reinigen, verwerken en optimaal voor te bereiden, zodat het uiteindelijke aluminiumproduct voldoet aan de vereiste kwaliteitsspecificaties. Vandaag de dag beschikken de meeste gieterijen wereldwijd nog niet over deze geavanceerde technologieën.
Traceerbaarheid van materialen door elke stap in de waardeketen — van schrootinzameling tot het eindproduct — is cruciaal. Dit vereist een volledige integratie van productiesystemen en ERP-software om elke stap te documenteren en transparantie te waarborgen. Dit maakt verifieerbare duurzaamheidsclaims mogelijk en zorgt voor naleving van industriestandaarden. Op dit moment zijn er slechts enkele aluminiumbedrijven wereldwijd die dit grondig aanpakken.
Verderop in de waardeketen werkt het concept van ‘lokaal geproduceerd’ alleen optimaal als er een wall-to-wall opstelling bestaat waarbij gieten en extrusie op dezelfde locatie plaatsvinden. De verdere bewerking en oppervlaktebehandeling gebeurt idealiter ter plaatse of wordt uitbesteed aan een lokale dienstverlener in de buurt, met nauwe samenwerking en geïntegreerde traceersystemen.
Moeilijk, maar niet onmogelijk
Oké, dat is een hele lijst: het opschalen van hyperlokale aluminiumwaardeketens naar massaproductie kent aanzienlijke uitdagingen. Maar het is wél haalbaar — mits de operationele, relationele en technologische obstakels die in dit artikel zijn genoemd, proactief worden aangepakt. Het label “lokaal geproduceerd” zou in de nabije toekomst zeker realiteit kunnen worden, al zal het zich in eerste instantie vooral beperken tot nicheproducten of eenmalige projecten. Op de lange termijn, wanneer er steeds meer schroot beschikbaar komt en waardeketens efficiënter worden, zou dit concept zomaar de nieuwe standaard kunnen worden voor duurzaam aluminium.