How AI is changing the geometry of aluminium extrusions
Artificial intelligence shows us that optimal design is not always what you’d intuitively expect.
As engineers, we're trained to chase the most efficient solutions: Lighter, stronger, lower cost. But for the last couple of years, as we’ve adopted more and more advanced modeling software that integrates artificial intelligence, I’ve come to realize that efficiency doesn’t always look the way you expect.
One recent case brought this into clear focus. We were exploring the design of an aluminium profile for a rear underrun protection device, which is a safety component used in large commercial vehicles to prevent cars from sliding underneath in a collision.
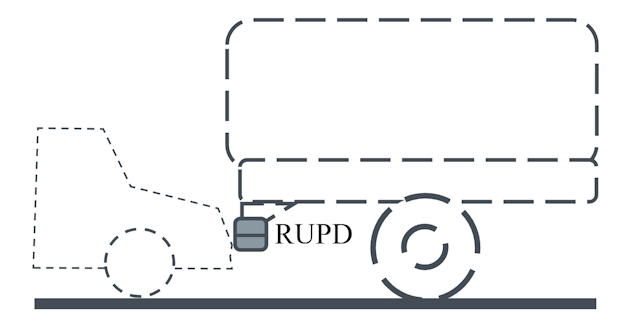
At first glance, the task was straightforward: Design a cross-section that could handle specific bending and crushing loads. But our challenge wasn’t just mechanical. We also had to factor in the cost of production and the carbon footprint of each piece.
Every decision has a chain reaction
That meant looking at the entire value chain: alloy composition, extrusion process and thermal treatments.
Each decision had cascading effects. For example, variability in alloy chemistry, especially with the silicon and magnesium contents, as well as impurities that affect the material’s strength and its behavior during processing.
Geometry as a design lever
We approached the problem with a methodology that uses advanced simulation and AI to model both mechanical performance and the manufacturing parameters. The geometry of the profile became our main lever. It was interesting to see how the geometry varied across different alloy compositions. For example, some compositions needed thicker walls or specific redistributions of material to meet strength requirements. In some cases, this meant adding mass where it mattered most, such as the corners of the profile, to enhance bending resistance.
What fascinated me was how these changes altered the perception of an “optimal” design.
If you looked only at weight or strength, the most efficient shape pointed one way. But once you factored in certain alloy compositions or production cost, the optimal solution shifted. It became a question of compromise: What performance are we optimizing for?
What it means to design with consequences
My take-away to this is that designing with different alloys demands a nuanced view. You have to think systemically, weighing trade-offs at every step. Even a small shift in composition can affect extrusion speed and mechanical properties.
What I took from this experience was a broader understanding of design. It’s no longer about finding the best shape. It’s about understanding the consequences of every choice. Material selection, geometry and process settings are all part of the same equation. And as sustainability becomes more central to what we do, the ability to navigate those trade-offs is becoming just as important as technical performance.
A smarter approach to aluminium design
We’ve also used this approach to help furniture company Flokk develop a new office chair made of aluminium with high post-consumer scrap content.
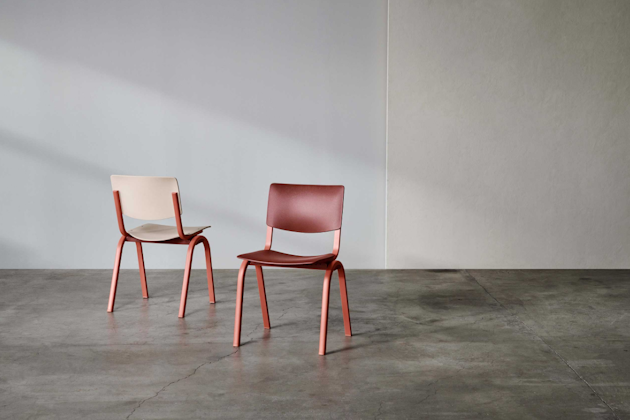
In the end, we were able to design a solution that met mechanical standards, controlled costs, and significantly reduced the CO₂ footprint. All by thinking differently about geometry and material. For me, that’s what it means to be designing with consequences. Not just building stronger or lighter, but smarter.